Whereas standard concrete and steel towers offer competitive prices in standard erection sites this is not generally the case in isolated locations or in water depths of over 10 m.
New structural solutions are possible by using advanced composite materials technology that may offer cheaper whole-life solutions by increasing the net area of commercially viable wind sites and prolong the life, or reduce the maintenance cost, of the wind generator superstructure.
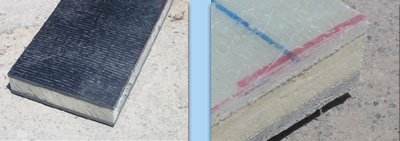
It is expected that a tower made from composite materials will have a number of advantages over a standard steel tower: lower maintenance costs, improved dynamic damping characteristics, extended fatigue life, reduced logistic costs for installation and, potentially, the capacity to improve on some aspects of environmental (landscape) pollution.
The aim of the MEGAWIND project was to provide an alternative to the existing steel or concrete designs particularly for cases where the site and accessibility conditions are difficult.
Within the MEGAWIND project on-site manufactured towers, featuring composite material shells and concrete or other core materials are introduced for application in the wind energy sector.
|
|
|
The design and development of an alternative wind turbine tower involved research on materials and large-scale structural tests on representative subassemblies of the tower.
The construction and manufacturing methodology aimed to reduce the logistic burden (heavy cranes and ancillary equipment), usually incurred when erecting towers made up of large monolithic elements.
The design approach to such a composite structure is based on the critical interaction between the design and the manufacturing process.
Different manufacturing solutions have been pursued during the course of the MEGAWIND project, in order to discern the optimum one.
|
|
|
The group comprising structural expert organizations, a construction company and a materials testing research laboratory, elaborated the conceptual design of the main structural elements of the tower and provided a tower design, based on the use of fiber-reinforced composites.
The dynamic and structural performance of the tower was initially verified by numerical simulation.
In addition to this, large-scale structural tests on representative subassemblies of the tower design were carried out before the approval of the final construction.
At a closing stage, the group gave extra emphasis on the optimization of the composite lamination sub-element joining as well as the manufacturing process.
The final wind turbine tower design was conducted according to the IEC 61400-1 standard using state-of-the-art tools, extensively validated in complex terrain applications.
A 40m height composite material tower was manufactured and the performance of the prototype was evaluated through systematic laboratory testing.
Test results were used for the design assessment of tower.
|
|
|
The success of the full-scale static test showed that composite material towers could present a viable solution within the wind energy sector, especially for the next generation wind turbines, or in cases were the cost of transport and installation could present a barrier in the exploitation of a specific site. Additionally, the innovative use of composite materials is also of interest for offshore applications.
In this case the advantages are those qualities that are afforded by the low chemical inertness of fiber-reinforced composites in saline environments, as well as the reduced logistic and transportation costs.
Although the tower design revolved around a land based tower, the advantages show that such constructions may offer new structural solutions for offshore platforms in waters over 10 m in depth.
|
|
|